The operation for Kiln 3 at a cement plant was stopped at 11.25pm due to red spot (brick failure). Investigation indicates that the air channel pipe was “missing”, which resulted in a distorted flame shape. This is because the primary function of the air channel pipe is said to shape the flame and swirl the air whilst introducing the coal dust, to enable efficient combustion. The team was informed that when the burner was opened up for checking /maintenance, the plate – i.e. the air channel pipe – was “missing”. This in turn caused the misalignment of the burner core, which then affected the flame in the Kiln. Interviews were conducted with the personnel in the Kiln Department, revealed that on the day of the incident; red-spot on the kiln was noted by the kiln operation personnel. However the flame in the kiln burner was continued until it was flamed off.”
- Current interruption occurs frequently, mainly due to power surges.
- A major power failure resulted in stopping the kiln operation for ½ day.
- Under normal circumstances of current interruption, kiln operation would be temporary stopped for ½ hour to an hour. After which the operation would resume, i.e. the kiln would be restarted.
- From the “Kiln Operation Log Sheet – Record Sheet”, it is noted that:
“Kiln was stopped due to current interruption. Further stopped as the computer monitor all totally blacked out…” During the interruption, the operator in the control room could not monitor the operating condition of the kiln, which resulted in the failure of automation control of the process from the control room. As such the process (kiln temperature) was controlled manually and Kiln 3 experienced a failure during this manual-controlled period. A detailed and thorough inspection revealed the following possibility for the failure of the kiln burner:
The inner tube of the burner gun, which was found protruding, moved out due to mechanical failure of the equipment, which in turn caused a misalignment of the core of the burner gun, subsequently causing an inconsistency in the shape of the flame. This caused the kiln brick to fail. The protrusion would then have given the impression that the plate was “missing”.
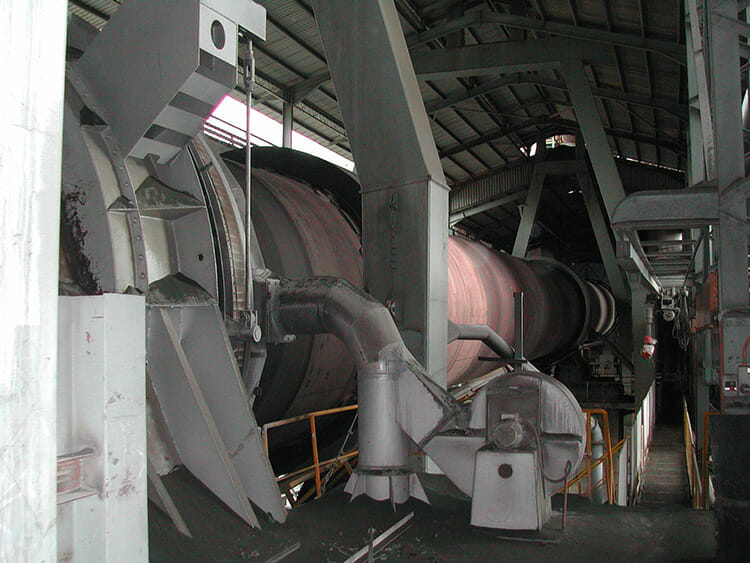
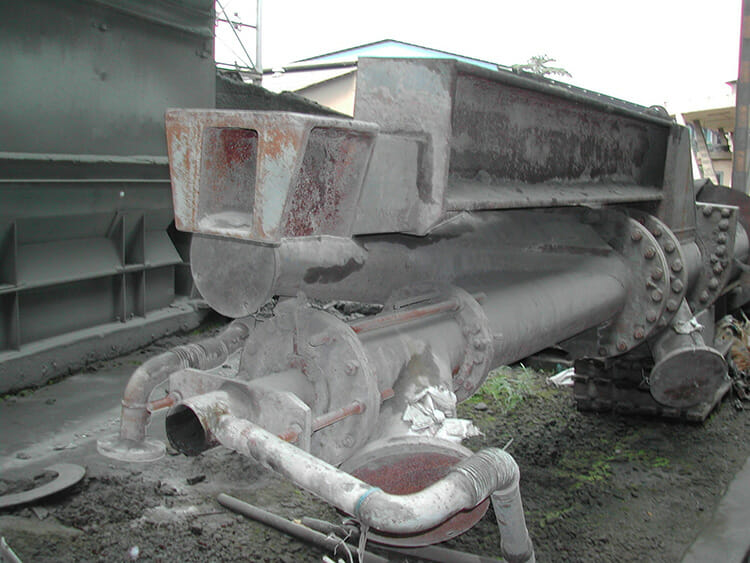
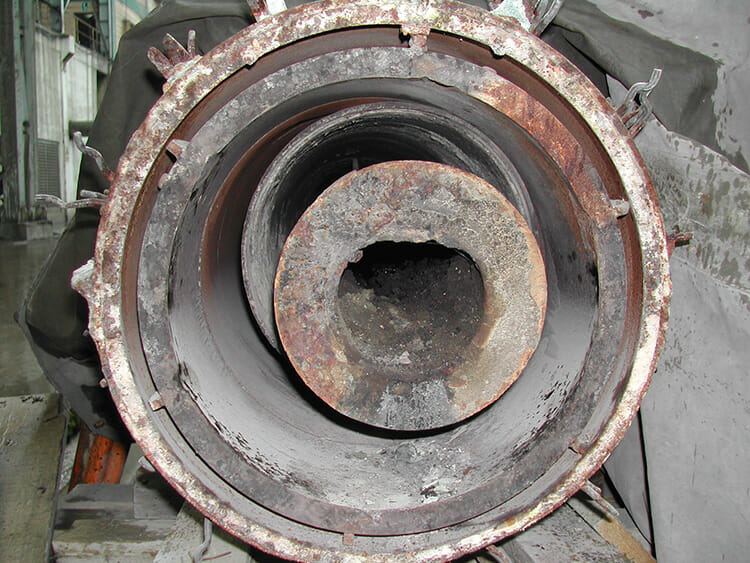
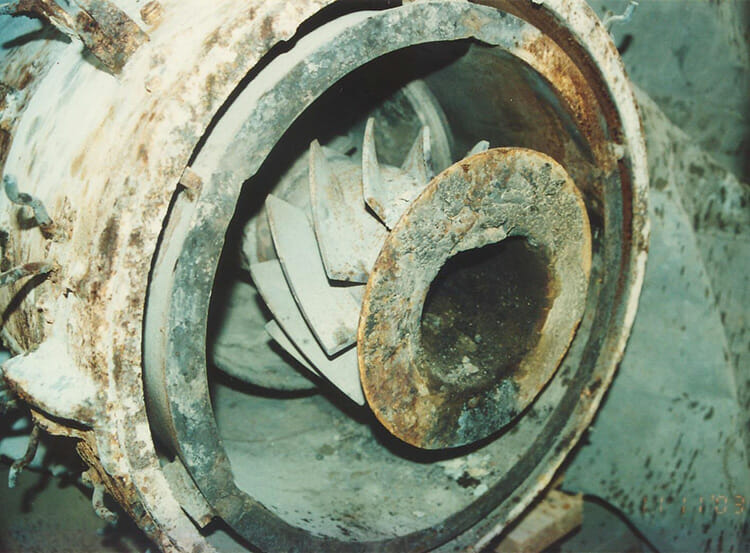
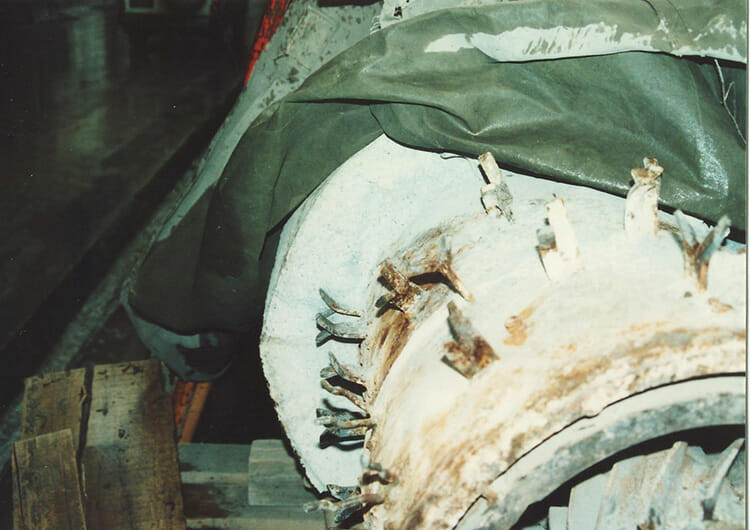
- Audio alert such as alarm to notify operators of any changes or operation upset of the kiln burner.
- Implementation of SOP (Standard Operating Procedure) when switching from automation to manual control.
- Enhance the flame monitoring system.
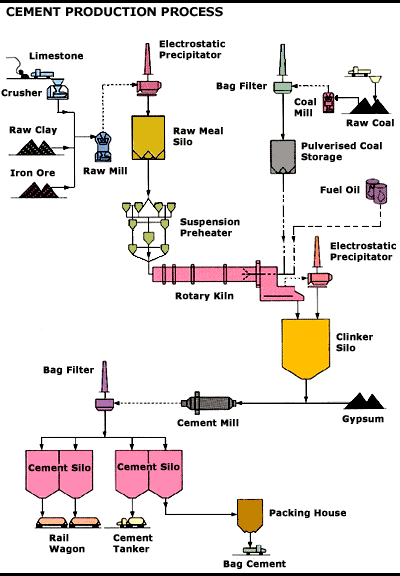
From the evidence and information available to the team, the failure of the kiln burner was that of the said “missing” plate (air channel pipe) was not “missing”, rather the protrusion of the inner tube created an impression that the plate was “missing”. This protrusion was due to an internal mechanical failure.